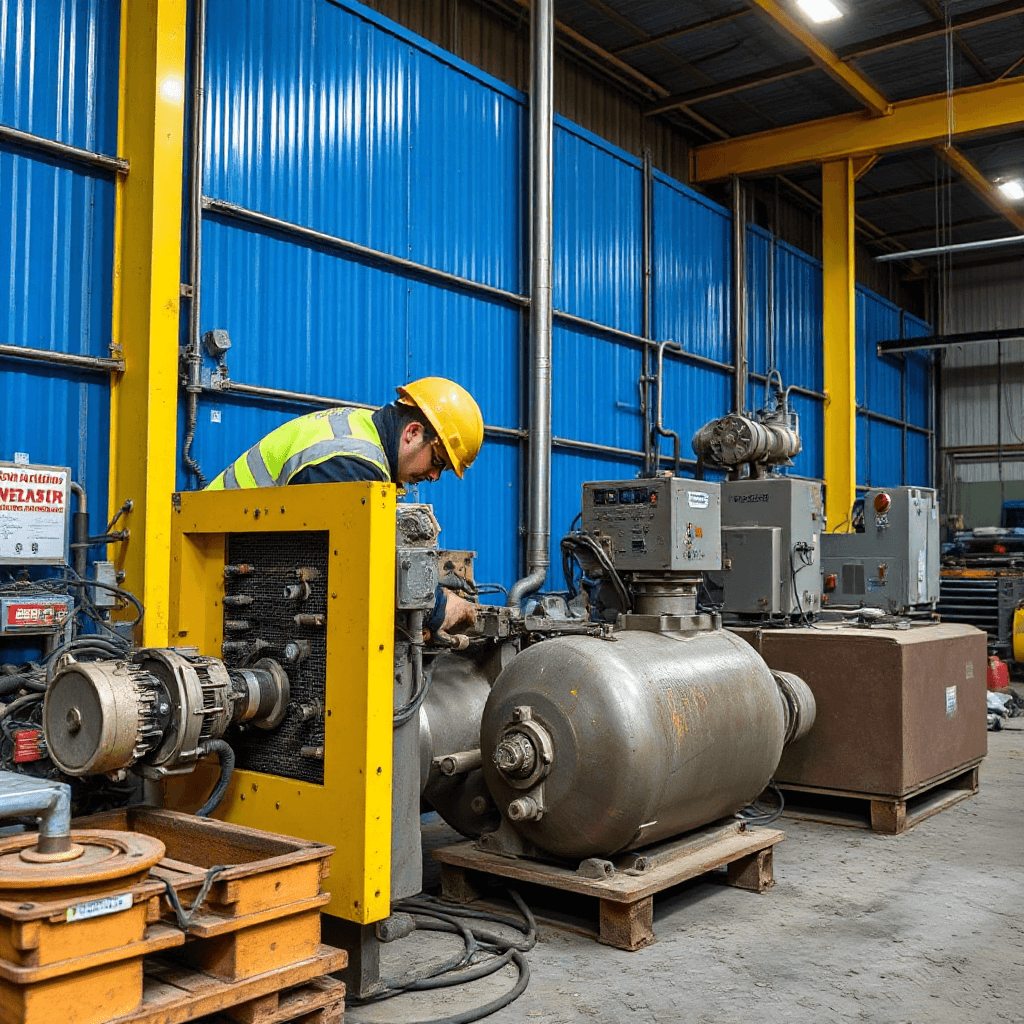
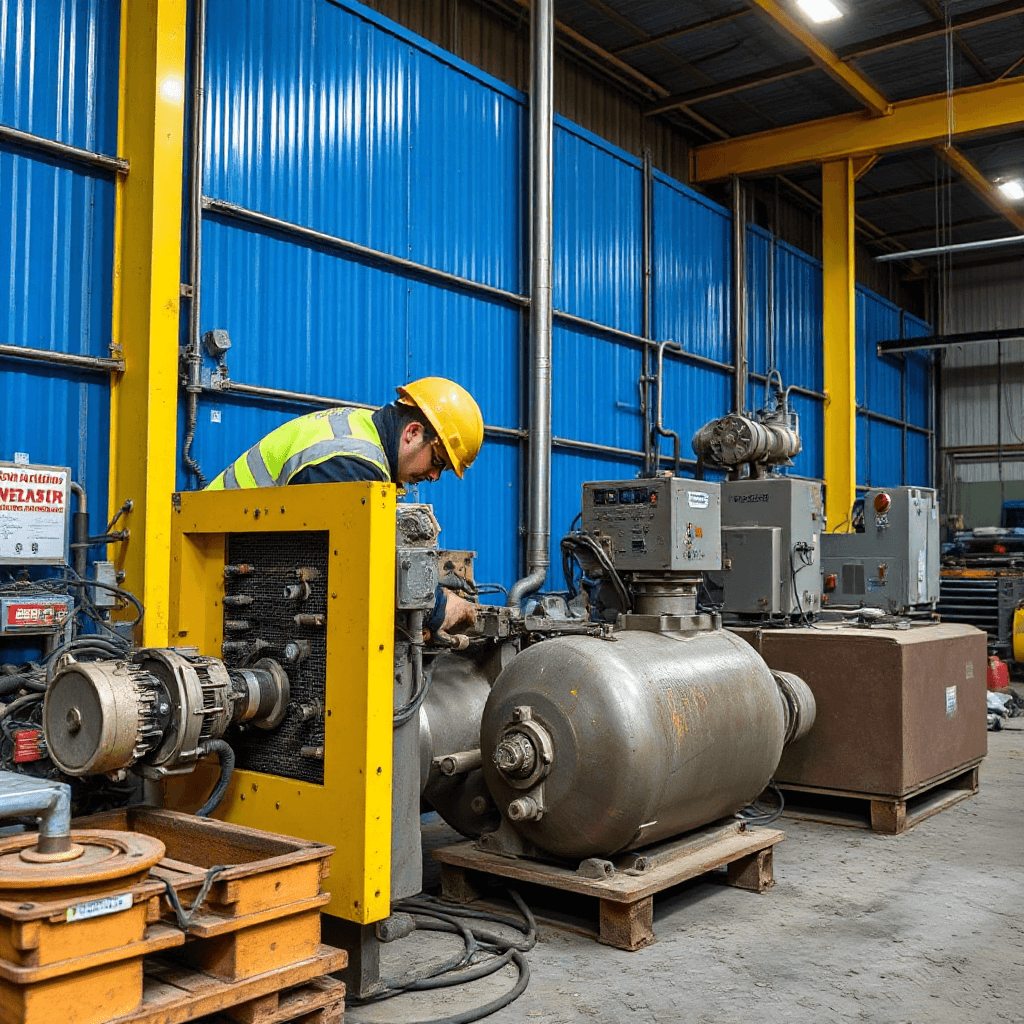
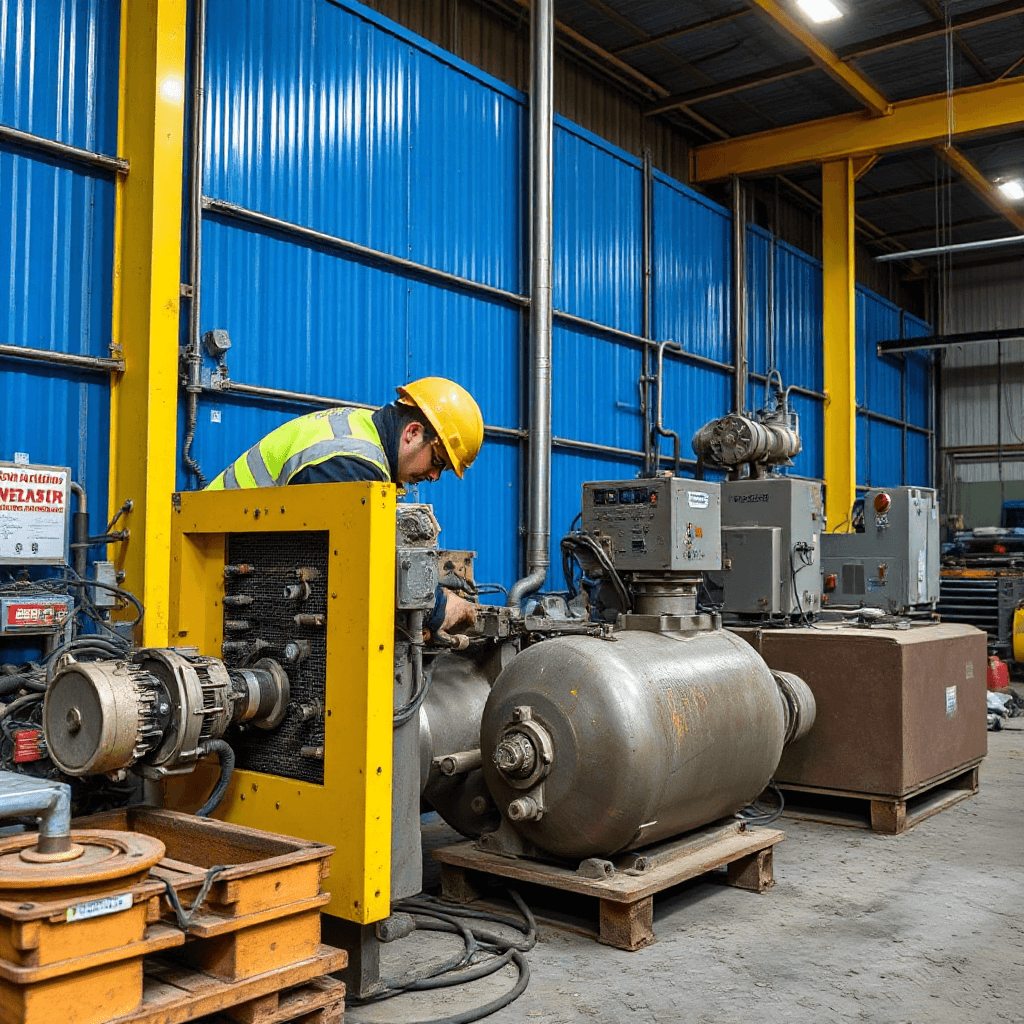
Kapsamlı bir Güvenilirlik Merkezli Bakım (RCM) programını hayata geçirmek, operasyonlarınızın çalışma süresini artıracak, ekipman güvenilirliğini yükseltecek ve bakım harcamalarını azaltacaktır. Eğer tam kapsamlı bir RCM programı mali imkânlarınızın ötesindeyse, 80/20 prensibini uygulayabilirsiniz. Bu prensibin temel düşüncesi şudur: Bakım kazancınızın %80'i, günlük olarak gerçekleştirdiğiniz önleyici eylemlerin sadece %20'sinden gelecektir. Yani, az sayıdaki kritik ve stratejik bakım faaliyeti, toplam performansınızın büyük kısmını belirleyecektir.
Makinelerinizin düzenli ve etkili bakımı, onlardan daha fazla verim almanızı ve daha uzun süre faydalanmanızı sağlar. Endüstride en üst düzey yaklaşım olarak kabul edilen Güvenilirlik Merkezli Bakım (RCM) sistemi, ideal bir çözüm sunsa da, uygulanması için ciddi bir bütçe ve yönetimsel kaynak gerektirir.
RCM sistemini kurmak şu an için işletmeniz açısından uygun değilse endişelenmeyin. Size burada, çok fazla maliyet gerektirmeden makine bakım süreçlerinizi iyileştirebileceğiniz sekiz temel prensip sunacağız.
1) Basit bir kondisyon izleme sistemi uygulayın
Çoğu ekipman, ciddi bir arızadan veya performans düşüşünden çok önce belirgin bozulma sinyalleri verir. Performans görünür şekilde etkilenmeden ve ürün kalitesi düşmeden, makine zaten sıkıntı yaşadığını size söyleyecektir.
Kondisyon izleme, bir makinedeki belirli koşulların gözlemlenmesi ve olası arızalara işaret edebilecek değişikliklerin tespit edilmesi anlamına gelir. Bu yaklaşım, potansiyel sorunları önceden fark etmenize ve bakım müdahalelerini zamanında planlamanıza olanak sağlar.
Kritik bir makine parçası için şu soruları yanıtlamanız gerekiyor:
Erken tehlike sinyallerini nasıl yakalayabilirim?
İzlemem gereken 1-2 temel parametre nedir?
Örneğin:
Titreşim seviyesi
Sıcaklık değişimleri
Gürültü düzeyi
Yağ kalitesi
Elektriksel tüketim
AirGemba'nın IoT ve yapay zeka destekli platformu, titreşim analizi gibi kondisyon izleme süreçlerini otomatikleştirerek:
Arızaları önceden tespit etmenize
Ekipman sağlığını gerçek zamanlı izlemenize
Tahmin edilebilir bakım stratejileri geliştirmenize
Beklenmedik duruş sürelerini minimize etmenize yardımcı olur
Bu yaklaşım, reaktif bakımdan proaktif bakıma geçişin anahtarıdır.
2) Operatörler için ekipman günlüklerini tanıtın ve eğitin
Makine operatörleriniz, arızaları önlemede en ön cephede yer alır. Her gün makinelerle çalıştıkları için, bir makinenin düzgün çalışıp çalışmadığını görünüşünden ve sesinden hemen anlayabilirler.
Ancak şu gerçeği de göz ardı edemeyiz: Ekipman arızalarının en yaygın sebeplerinden biri operatör hatalarıdır. Bu yüzden tüm operatörlerin makineleri doğru kullanması hayati önem taşır.
Bunu sağlamak için şunları yapmanızı öneriyoruz:
Öncelikle, güvenli ve verimli makine kullanımı için standart bir çalışma prosedürü oluşturun ve operatörlerinizi bu konuda eğitin. Onlara sık karşılaşılan sorunları nasıl fark edeceklerini öğretin. Temizlik ve yağlama gibi günlük basit bakım işlerini de sorumlulukları arasına ekleyin. Kısacası, bakım sorumluluğunun bir kısmını operatörlere devrederek 'otonom bakım' sistemine geçmeyi hedefleyin.
Operatörlerin işini kolaylaştırmak için makine günlüğü sistemi kurun. Bu günlüklere gözlemlerini, endişelerini ve karşılaştıkları sorunları not edebilsinler. Bakım ekibiniz bu günlükleri her gün kontrol etmeli ve notları şu üç kategoriden birine göre değerlendirmelidir:
Önemsiz bir durum - herhangi bir işlem gerektirmez
Hemen çözülebilecek basit bir sorun - teknisyen hemen müdahale eder
Planlı bakımda ele alınması gereken bir konu - bakım planına eklenir ve takip için iş emri numarası günlüğe işlenir
3) Planlı bakım görev kitleri geliştirin
Planlı bakımlarda genellikle aynı parçalar ve sarf malzemeleri tekrar tekrar kullanılır. Bu durumda, teknisyenin her bakım öncesi gerekli malzemeleri tek tek toplaması yerine, daha pratik bir yöntem öneriyoruz:
Bakım kitleri hazırlayın. Her kit, belirli bir bakım görevi için gereken tüm parça ve malzemeleri içersin. Bu kitlere özel parça numaraları verin ve planlı bakım formlarında bu numaraları kullanın. Böylece hem takip kolaylaşır, hem de karışıklık riski azalır.
Bu sistem sayesinde, bir bakım planlandığında depo görevliniz ilgili kiti raftan alıp hazırlayabilir. Bakım günü geldiğinde de teknisyenleriniz, o gün yapacakları tüm bakım işleri için gereken kitleri toplu halde teslim alır ve vakit kaybetmeden işe başlayabilir."
Bu düzenlemede ana fikri korurken, daha doğal bir Türkçe anlatım kullandım ve içeriği daha organize bir şekilde sundum. Teknik terimleri muhafaza ederken, anlatımı daha akıcı hale getirdim.
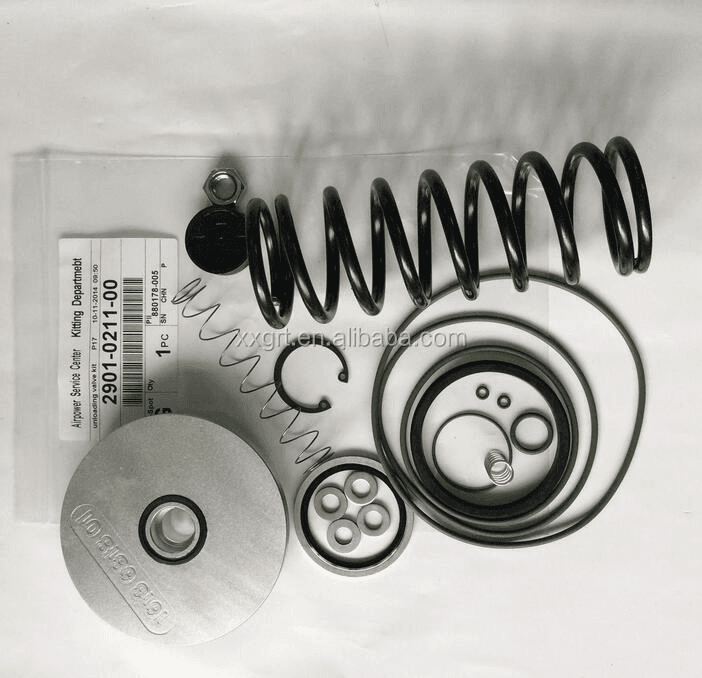
FS 8000H OEM Hava Kompresörü için önleyici bakım kiti.
Önceden hazırlanmış bakım kitleri, birçok açıdan işinizi kolaylaştırır. Öncelikle, planlı bakım başlamadan önce tüm gerekli malzemelerin elinizin altında olmasını sağlar. Bu da teknisyenlerinizin zamanını verimli kullanmalarına yardımcı olur.
Dahası, bu sistem sayesinde yağlama veya conta değiştirme gibi küçük ama kritik bakım işleri de atlanmaz. Çünkü teknisyenin eksik malzeme aramak için atölyeden ayrılması gerekmez ve tüm işler planlandığı gibi yapılabilir.
4) Performans metriklerini takip edin
Bakım programınızın verimli çalıştığını düşünseniz bile, düzenli bakım işlemlerini aksatmak, uzun vadede makinelerinizin güvenilirliğini ve ömrünü ciddi şekilde etkileyebilir. İdeal bir senaryoda, önleyici bakımı düzenli yaparak sadece birkaç acil müdahale gerektiren arıza ile karşılaşırız.
Ancak gerçek hayatta, güvenilmez ekipmanlarla uğraşırken daha sık arızalarla karşılaşmak kaçınılmaz oluyor. Bakım performansını izlemek, planlı bakım görevlerinin tam zamanında ve gerekli sıklıkta yapılıp yapılmadığını anlamak için çok önemli bir yöntem.
Bu izleme sayesinde, bakım iş listenizdeki görevlerin tamamlanma durumunu ve ekipmanlarınızın toplam arıza sürelerini net bir şekilde görebilirsiniz. Ayrıca, sık yaşanan arızaları tespit edebilir ve buna göre önlemler alabilirsiniz. Bu bilgileri kullanarak, önleyici bakım sıklığını artırabilir veya ekipmanlarınızın güvenilirliğini yükseltecek ek çalışmalar yapabilirsiniz.
İşte bakım performansınızı değerlendirebileceğiniz beş temel gösterge:
Aylık olarak planlanan bakım görevlerine kıyasla tamamlanan görev sayısı
Aylık meydana gelen arıza sayısı
Arızaların ekipman türüne veya konumuna göre nedenleri
Aylık olarak bakım iş listesine eklenen ve çıkarılan görev sayısı
Ortalama arıza onarım süresi (MTTR) ve ortalama arıza aralığı (MTBF)
Bu bakım metriklerini düzenli olarak takip ederek, bakım stratejinizin gelişip gelişmediğini veya gerilediğini görebilirsiniz. Böylece, sisteminizdeki potansiyel sorunları erkenden tespit edebilir ve gerekli düzeltmeleri yapabilirsiniz.
5) Modern bir CMMS ile makine bakımını kolaylaştırın
Ekipman performansınız ve bakım prosedürleriniz hakkında veri toplayamıyorsanız, esasen gözü bağlı bir şekilde çalışıyor ve operasyonunuzu optimize etmek için boşuna çırpınıyorsunuz demektir. Bilgisayar destekli bir bakım yönetim sistemini (CMMS) uygulamak, birkaç yıl öncesine kıyasla artık çok daha kolay. Üstelik bakım performansınız hakkında elde edeceğiniz içgörüler, yatırımın karşılığını fazlasıyla verecek.
Modern bir CMMS'ye geçmek, operasyonel verileri yakalamaya ve bakım faaliyetlerini yönetmeye başlamanın uygun maliyetli ve etkili bir yoludur. Günümüz bulut tabanlı bakım yazılımları, işletmelere oldukça güçlü özellikler sunuyor:
Önleyici bakım takvimi ve zamanlaması: Bakım işlemlerinizi önceden planlamanıza ve düzenli olarak gerçekleştirmenize olanak sağlar.
Yedek parça envanter yönetimi: Stok durumunuzu anında görmenizi ve parça eksikliği riskini minimize etmenizi sağlar.
Varlık Yönetimi: Tüm ekipmanlarınızın yaşam döngüsünü izlemenize ve performanslarını takip etmenize yardımcı olur.
İş emri yönetimi: Bakım görevlerinin atanması, takibi ve tamamlanması süreçlerini kolaylaştırır.
Detaylı Raporlama: Performans ve bakım verilerinizi analiz etmenize olanak tanır.
Üstelik modern CMMS sistemleri, finans ve insan kaynakları gibi diğer iş çözümleriyle de entegre olabilmektedir. Dahası, makine sensörlerinden gerçek zamanlı veri toplama özelliği sayesinde, ekipmanlarınızın durumunu anında izleyebilirsiniz.
6) Planlı Bakım görevlerini optimize edin
Planlı bakım görevleri genellikle "kur ve unut" yaklaşımıyla ele alınır - bir kez oluşturulduktan sonra neredeyse hiç gözden geçirilmezler. Oysa tüm planlı bakım görevlerini sürekli olarak gözden geçirmek, bakım stratejinizin en kritik parçasıdır.
Her bir bakım görevini aşağıdaki açılardan düzenli olarak değerlendirmek şart:
Güncelliği: Bu göreve hâlâ ihtiyaç var mı? Eğer artık gerekli değilse, derhal listeden çıkarın.
Etkinliği: Tanımlanan görev gerçekten en etkili yaklaşım mı? Belki de süreç daha fazla ayrıntıya veya daha az adıma ihtiyaç duyuyor olabilir.
Verimliliği: Görevi daha optimize edebilir misiniz? Aynı sonucu daha az kaynak ve zamanda elde etmenin yolları var mı?
Doğruluğu: Görev, doğru teknik kılavuzlara ve gerekli yedek parça bilgilerine mi atıfta bulunuyor?
Planlama Süresi: Göreve ayrılan zaman gerçekçi mi? Fazla mı tahmin edilmiş yoksa eksik mi planlanmış? Ayrıca, bu görevi gerçekleştirecek personel hâlâ uygun ve yetkin mi?
Görev Çakışmaları: Benzer veya örtüşen başka görevler var mı? Belki bunları birleştirmenin zamanı gelmiştir.
Eksik Alanlar: Verileriniz yeni bir önleyici bakım görevine ihtiyaç olduğunu mı gösteriyor? Henüz bakım kapsamına alınmamış ekipmanlar var mı?
Optimize etme sürecinde, standartlaştırılabilecek görevleri belirleyin. Bunun için özel önleyici bakım kontrol listeleri oluşturun ve bunları bakım planlarınıza entegre edin.
Sürekli iyileştirme kültürünü benimsemek, bakım programınızda küçük ama sürekli güncellemeler yapmanıza olanak sağlar. Bu yaklaşım, bakım yatırımınızdan maksimum verimi almanızın anahtarıdır.
7) Bir yağlama programı oluşturun
Yağlamayı sıradan bakım görevlerinin içine gömmek yerine, her ekipmanın zamanında ve doğru şekilde yağlanmasını sağlayacak bağımsız bir yağlama programı oluşturmak çok önemlidir. Böyle bir program, ekipmanlarınızın performansını ve ömrünü doğrudan etkileyecektir.
Kapsamlı bir yağlama programı oluşturmak için şu adımları izleyin:
Yağlama Noktalarının Tespiti: Tüm yağlama noktalarını detaylı bir şekilde tespit edin, kaydedin ve haritalandırın. Bu süreç özellikle eski makinelerde oldukça zahmetli olabilir, ancak mutlaka yapılması gereken bir çalışmadır.
Dinamik Yağlama Planlaması: Makine çalışma saatlerini ve üretim döngülerini dikkate alın. Yağlama ihtiyacı, makine kullanım yoğunluğuna ve türüne bağlı olarak değişkenlik gösterir.
Yağ Değişimi ve Analizi: Her yağ değişimini programınıza dahil edin. Alınan yağ numunelerinin sonuçlarını düzenli olarak analiz edin. Bu, olası arızaların erken tespitine yardımcı olacaktır.
Doğru Yağlayıcı Seçimi: Her ekipman için:
Uygun yağlayıcı türünü belirleyin
Gerekli yağlayıcı miktarını tespit edin
Yağlama prosedürünü net bir şekilde tanımlayın
Düzeltici Bakım: Yağlama noktalarında herhangi bir hasar, tıkanıklık veya deformasyon tespit edildiğinde hemen müdahale edilmesini sağlayın.
Maksimum ekipman ömrüne ulaşmak birçok faktöre bağlı olsa da, güvenilirliği artıran en temel eylemlerden biri kesinlikle kapsamlı ve sistematik bir yağlama programıdır. Bu programa yatırım yapmak, uzun vadede ciddi maliyet tasarrufları ve performans artışı sağlayacaktır.
8) Pompa ve dişli kutularında yumuşak ayak analizi ve mil hizalaması yapın
Dönen makinelerde şaft hizalamasındaki hatalar, işletmeniz için ciddi sonuçlar doğurabilecek bir dizi probleme yol açar. Yanlış hizalanmış bir şaft, bakım maliyetlerinizi artırırken ekipmanınızın ömrünü de önemli ölçüde kısaltır.
Şaft hizalama hatalarının neden olduğu başlıca sorunlar şunlardır:
Makine genelinde artan titreşimler
Conta ve yataklarda aşırı ve hızlanmış aşınma
Mil veya kaplinde meydana gelen yapısal arızalar
Ekipman içindeki sürtünmenin artması
Daha yüksek enerji tüketimi
Yağ sızıntılarında artış
Civatalarda gevşeme
Kayış sistemlerinde aşınma ve beklenmedik arızalar
Şaft hizalaması öncesinde ve sırasında mutlaka "yumuşak ayak" analizini gerçekleştirmelisiniz. Yumuşak ayak terimi, dönen ekipmanın bir veya daha fazla ayağının montaj plakasıyla tam temas etmemesi durumunu tanımlar. Düzgün desteklenmeyen montaj parçaları, çalışma sırasında çatlayabilir ve bu durum hem hizalama sorunlarına hem de aşırı titreşimlere neden olabilir.
Pompa veya dişli kutusu montajlarında lazer hizalama sistemlerini kullanmak, yumuşak ayak problemlerini çözmek ve mükemmel şaft hizalaması elde etmek için en etkili yöntemdir. Doğru bir hizalama, dönen ekipmanınızın ömrünü uzatır, erken arızaları önler ve toplam bakım sürelerini önemli ölçüde azaltır.
Bu örnek, endüstriyel makine bakımının, plansız duruş sürelerini minimize etmenin yanı sıra etkin ekipman yönetiminin temel hedeflerine nasıl katkıda bulunduğunu mükemmel bir şekilde göstermektedir.
Makine Bakımını Bir Üst Seviyeye Taşımak
Kapsamlı bir Güvenilirlik Merkezli Bakım (RCM) programını hayata geçirmek, operasyonlarınızın çalışma süresini artıracak, ekipman güvenilirliğini yükseltecek ve bakım harcamalarını azaltacaktır. Eğer tam kapsamlı bir RCM programı mali imkânlarınızın ötesindeyse, 80/20 prensibini uygulayabilirsiniz.
Bu prensibin temel düşüncesi şudur: Bakım kazancınızın %80'i, günlük olarak gerçekleştirdiğiniz önleyici eylemlerin sadece %20'sinden gelecektir. Yani, az sayıdaki kritik ve stratejik bakım faaliyeti, toplam performansınızın büyük kısmını belirleyecektir.
Etkili bir bakım programının temelini oluşturan ve bireysel olarak uygulayabileceğiniz temel stratejileri özetledik. Bu yaklaşımlar, bakım yönetimini dönüştürebilir ve operasyonel verimliliğinizi önemli ölçüde artırabilir.
Limble CMMS, bakım bakımını organize etmek, otomatikleştirmek ve kolaylaştırmak için tasarlanmıştır. Nasıl yapılacağını öğrenmek için bir demo talep edin , ücretsiz bir deneme başlatın.
Makinelerinizin düzenli ve etkili bakımı, onlardan daha fazla verim almanızı ve daha uzun süre faydalanmanızı sağlar. Endüstride en üst düzey yaklaşım olarak kabul edilen Güvenilirlik Merkezli Bakım (RCM) sistemi, ideal bir çözüm sunsa da, uygulanması için ciddi bir bütçe ve yönetimsel kaynak gerektirir.
RCM sistemini kurmak şu an için işletmeniz açısından uygun değilse endişelenmeyin. Size burada, çok fazla maliyet gerektirmeden makine bakım süreçlerinizi iyileştirebileceğiniz sekiz temel prensip sunacağız.
1) Basit bir kondisyon izleme sistemi uygulayın
Çoğu ekipman, ciddi bir arızadan veya performans düşüşünden çok önce belirgin bozulma sinyalleri verir. Performans görünür şekilde etkilenmeden ve ürün kalitesi düşmeden, makine zaten sıkıntı yaşadığını size söyleyecektir.
Kondisyon izleme, bir makinedeki belirli koşulların gözlemlenmesi ve olası arızalara işaret edebilecek değişikliklerin tespit edilmesi anlamına gelir. Bu yaklaşım, potansiyel sorunları önceden fark etmenize ve bakım müdahalelerini zamanında planlamanıza olanak sağlar.
Kritik bir makine parçası için şu soruları yanıtlamanız gerekiyor:
Erken tehlike sinyallerini nasıl yakalayabilirim?
İzlemem gereken 1-2 temel parametre nedir?
Örneğin:
Titreşim seviyesi
Sıcaklık değişimleri
Gürültü düzeyi
Yağ kalitesi
Elektriksel tüketim
AirGemba'nın IoT ve yapay zeka destekli platformu, titreşim analizi gibi kondisyon izleme süreçlerini otomatikleştirerek:
Arızaları önceden tespit etmenize
Ekipman sağlığını gerçek zamanlı izlemenize
Tahmin edilebilir bakım stratejileri geliştirmenize
Beklenmedik duruş sürelerini minimize etmenize yardımcı olur
Bu yaklaşım, reaktif bakımdan proaktif bakıma geçişin anahtarıdır.
2) Operatörler için ekipman günlüklerini tanıtın ve eğitin
Makine operatörleriniz, arızaları önlemede en ön cephede yer alır. Her gün makinelerle çalıştıkları için, bir makinenin düzgün çalışıp çalışmadığını görünüşünden ve sesinden hemen anlayabilirler.
Ancak şu gerçeği de göz ardı edemeyiz: Ekipman arızalarının en yaygın sebeplerinden biri operatör hatalarıdır. Bu yüzden tüm operatörlerin makineleri doğru kullanması hayati önem taşır.
Bunu sağlamak için şunları yapmanızı öneriyoruz:
Öncelikle, güvenli ve verimli makine kullanımı için standart bir çalışma prosedürü oluşturun ve operatörlerinizi bu konuda eğitin. Onlara sık karşılaşılan sorunları nasıl fark edeceklerini öğretin. Temizlik ve yağlama gibi günlük basit bakım işlerini de sorumlulukları arasına ekleyin. Kısacası, bakım sorumluluğunun bir kısmını operatörlere devrederek 'otonom bakım' sistemine geçmeyi hedefleyin.
Operatörlerin işini kolaylaştırmak için makine günlüğü sistemi kurun. Bu günlüklere gözlemlerini, endişelerini ve karşılaştıkları sorunları not edebilsinler. Bakım ekibiniz bu günlükleri her gün kontrol etmeli ve notları şu üç kategoriden birine göre değerlendirmelidir:
Önemsiz bir durum - herhangi bir işlem gerektirmez
Hemen çözülebilecek basit bir sorun - teknisyen hemen müdahale eder
Planlı bakımda ele alınması gereken bir konu - bakım planına eklenir ve takip için iş emri numarası günlüğe işlenir
3) Planlı bakım görev kitleri geliştirin
Planlı bakımlarda genellikle aynı parçalar ve sarf malzemeleri tekrar tekrar kullanılır. Bu durumda, teknisyenin her bakım öncesi gerekli malzemeleri tek tek toplaması yerine, daha pratik bir yöntem öneriyoruz:
Bakım kitleri hazırlayın. Her kit, belirli bir bakım görevi için gereken tüm parça ve malzemeleri içersin. Bu kitlere özel parça numaraları verin ve planlı bakım formlarında bu numaraları kullanın. Böylece hem takip kolaylaşır, hem de karışıklık riski azalır.
Bu sistem sayesinde, bir bakım planlandığında depo görevliniz ilgili kiti raftan alıp hazırlayabilir. Bakım günü geldiğinde de teknisyenleriniz, o gün yapacakları tüm bakım işleri için gereken kitleri toplu halde teslim alır ve vakit kaybetmeden işe başlayabilir."
Bu düzenlemede ana fikri korurken, daha doğal bir Türkçe anlatım kullandım ve içeriği daha organize bir şekilde sundum. Teknik terimleri muhafaza ederken, anlatımı daha akıcı hale getirdim.
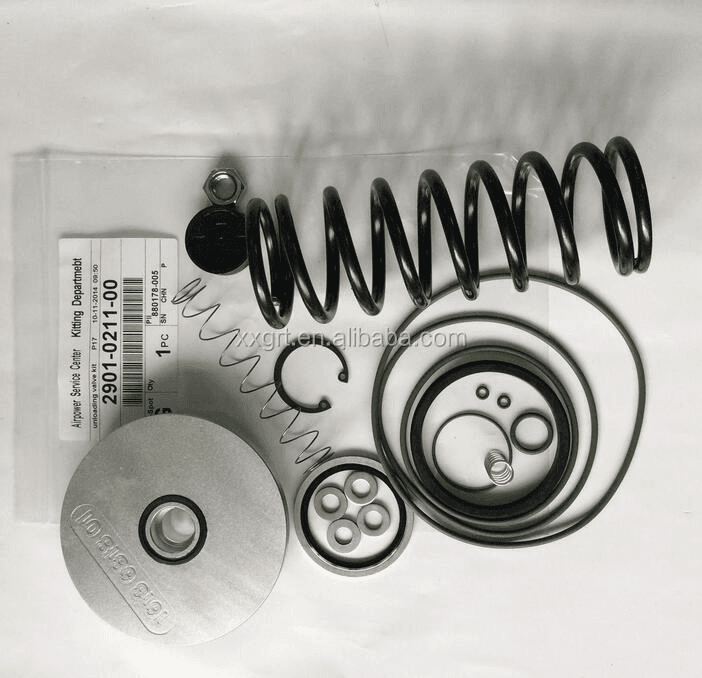
FS 8000H OEM Hava Kompresörü için önleyici bakım kiti.
Önceden hazırlanmış bakım kitleri, birçok açıdan işinizi kolaylaştırır. Öncelikle, planlı bakım başlamadan önce tüm gerekli malzemelerin elinizin altında olmasını sağlar. Bu da teknisyenlerinizin zamanını verimli kullanmalarına yardımcı olur.
Dahası, bu sistem sayesinde yağlama veya conta değiştirme gibi küçük ama kritik bakım işleri de atlanmaz. Çünkü teknisyenin eksik malzeme aramak için atölyeden ayrılması gerekmez ve tüm işler planlandığı gibi yapılabilir.
4) Performans metriklerini takip edin
Bakım programınızın verimli çalıştığını düşünseniz bile, düzenli bakım işlemlerini aksatmak, uzun vadede makinelerinizin güvenilirliğini ve ömrünü ciddi şekilde etkileyebilir. İdeal bir senaryoda, önleyici bakımı düzenli yaparak sadece birkaç acil müdahale gerektiren arıza ile karşılaşırız.
Ancak gerçek hayatta, güvenilmez ekipmanlarla uğraşırken daha sık arızalarla karşılaşmak kaçınılmaz oluyor. Bakım performansını izlemek, planlı bakım görevlerinin tam zamanında ve gerekli sıklıkta yapılıp yapılmadığını anlamak için çok önemli bir yöntem.
Bu izleme sayesinde, bakım iş listenizdeki görevlerin tamamlanma durumunu ve ekipmanlarınızın toplam arıza sürelerini net bir şekilde görebilirsiniz. Ayrıca, sık yaşanan arızaları tespit edebilir ve buna göre önlemler alabilirsiniz. Bu bilgileri kullanarak, önleyici bakım sıklığını artırabilir veya ekipmanlarınızın güvenilirliğini yükseltecek ek çalışmalar yapabilirsiniz.
İşte bakım performansınızı değerlendirebileceğiniz beş temel gösterge:
Aylık olarak planlanan bakım görevlerine kıyasla tamamlanan görev sayısı
Aylık meydana gelen arıza sayısı
Arızaların ekipman türüne veya konumuna göre nedenleri
Aylık olarak bakım iş listesine eklenen ve çıkarılan görev sayısı
Ortalama arıza onarım süresi (MTTR) ve ortalama arıza aralığı (MTBF)
Bu bakım metriklerini düzenli olarak takip ederek, bakım stratejinizin gelişip gelişmediğini veya gerilediğini görebilirsiniz. Böylece, sisteminizdeki potansiyel sorunları erkenden tespit edebilir ve gerekli düzeltmeleri yapabilirsiniz.
5) Modern bir CMMS ile makine bakımını kolaylaştırın
Ekipman performansınız ve bakım prosedürleriniz hakkında veri toplayamıyorsanız, esasen gözü bağlı bir şekilde çalışıyor ve operasyonunuzu optimize etmek için boşuna çırpınıyorsunuz demektir. Bilgisayar destekli bir bakım yönetim sistemini (CMMS) uygulamak, birkaç yıl öncesine kıyasla artık çok daha kolay. Üstelik bakım performansınız hakkında elde edeceğiniz içgörüler, yatırımın karşılığını fazlasıyla verecek.
Modern bir CMMS'ye geçmek, operasyonel verileri yakalamaya ve bakım faaliyetlerini yönetmeye başlamanın uygun maliyetli ve etkili bir yoludur. Günümüz bulut tabanlı bakım yazılımları, işletmelere oldukça güçlü özellikler sunuyor:
Önleyici bakım takvimi ve zamanlaması: Bakım işlemlerinizi önceden planlamanıza ve düzenli olarak gerçekleştirmenize olanak sağlar.
Yedek parça envanter yönetimi: Stok durumunuzu anında görmenizi ve parça eksikliği riskini minimize etmenizi sağlar.
Varlık Yönetimi: Tüm ekipmanlarınızın yaşam döngüsünü izlemenize ve performanslarını takip etmenize yardımcı olur.
İş emri yönetimi: Bakım görevlerinin atanması, takibi ve tamamlanması süreçlerini kolaylaştırır.
Detaylı Raporlama: Performans ve bakım verilerinizi analiz etmenize olanak tanır.
Üstelik modern CMMS sistemleri, finans ve insan kaynakları gibi diğer iş çözümleriyle de entegre olabilmektedir. Dahası, makine sensörlerinden gerçek zamanlı veri toplama özelliği sayesinde, ekipmanlarınızın durumunu anında izleyebilirsiniz.
6) Planlı Bakım görevlerini optimize edin
Planlı bakım görevleri genellikle "kur ve unut" yaklaşımıyla ele alınır - bir kez oluşturulduktan sonra neredeyse hiç gözden geçirilmezler. Oysa tüm planlı bakım görevlerini sürekli olarak gözden geçirmek, bakım stratejinizin en kritik parçasıdır.
Her bir bakım görevini aşağıdaki açılardan düzenli olarak değerlendirmek şart:
Güncelliği: Bu göreve hâlâ ihtiyaç var mı? Eğer artık gerekli değilse, derhal listeden çıkarın.
Etkinliği: Tanımlanan görev gerçekten en etkili yaklaşım mı? Belki de süreç daha fazla ayrıntıya veya daha az adıma ihtiyaç duyuyor olabilir.
Verimliliği: Görevi daha optimize edebilir misiniz? Aynı sonucu daha az kaynak ve zamanda elde etmenin yolları var mı?
Doğruluğu: Görev, doğru teknik kılavuzlara ve gerekli yedek parça bilgilerine mi atıfta bulunuyor?
Planlama Süresi: Göreve ayrılan zaman gerçekçi mi? Fazla mı tahmin edilmiş yoksa eksik mi planlanmış? Ayrıca, bu görevi gerçekleştirecek personel hâlâ uygun ve yetkin mi?
Görev Çakışmaları: Benzer veya örtüşen başka görevler var mı? Belki bunları birleştirmenin zamanı gelmiştir.
Eksik Alanlar: Verileriniz yeni bir önleyici bakım görevine ihtiyaç olduğunu mı gösteriyor? Henüz bakım kapsamına alınmamış ekipmanlar var mı?
Optimize etme sürecinde, standartlaştırılabilecek görevleri belirleyin. Bunun için özel önleyici bakım kontrol listeleri oluşturun ve bunları bakım planlarınıza entegre edin.
Sürekli iyileştirme kültürünü benimsemek, bakım programınızda küçük ama sürekli güncellemeler yapmanıza olanak sağlar. Bu yaklaşım, bakım yatırımınızdan maksimum verimi almanızın anahtarıdır.
7) Bir yağlama programı oluşturun
Yağlamayı sıradan bakım görevlerinin içine gömmek yerine, her ekipmanın zamanında ve doğru şekilde yağlanmasını sağlayacak bağımsız bir yağlama programı oluşturmak çok önemlidir. Böyle bir program, ekipmanlarınızın performansını ve ömrünü doğrudan etkileyecektir.
Kapsamlı bir yağlama programı oluşturmak için şu adımları izleyin:
Yağlama Noktalarının Tespiti: Tüm yağlama noktalarını detaylı bir şekilde tespit edin, kaydedin ve haritalandırın. Bu süreç özellikle eski makinelerde oldukça zahmetli olabilir, ancak mutlaka yapılması gereken bir çalışmadır.
Dinamik Yağlama Planlaması: Makine çalışma saatlerini ve üretim döngülerini dikkate alın. Yağlama ihtiyacı, makine kullanım yoğunluğuna ve türüne bağlı olarak değişkenlik gösterir.
Yağ Değişimi ve Analizi: Her yağ değişimini programınıza dahil edin. Alınan yağ numunelerinin sonuçlarını düzenli olarak analiz edin. Bu, olası arızaların erken tespitine yardımcı olacaktır.
Doğru Yağlayıcı Seçimi: Her ekipman için:
Uygun yağlayıcı türünü belirleyin
Gerekli yağlayıcı miktarını tespit edin
Yağlama prosedürünü net bir şekilde tanımlayın
Düzeltici Bakım: Yağlama noktalarında herhangi bir hasar, tıkanıklık veya deformasyon tespit edildiğinde hemen müdahale edilmesini sağlayın.
Maksimum ekipman ömrüne ulaşmak birçok faktöre bağlı olsa da, güvenilirliği artıran en temel eylemlerden biri kesinlikle kapsamlı ve sistematik bir yağlama programıdır. Bu programa yatırım yapmak, uzun vadede ciddi maliyet tasarrufları ve performans artışı sağlayacaktır.
8) Pompa ve dişli kutularında yumuşak ayak analizi ve mil hizalaması yapın
Dönen makinelerde şaft hizalamasındaki hatalar, işletmeniz için ciddi sonuçlar doğurabilecek bir dizi probleme yol açar. Yanlış hizalanmış bir şaft, bakım maliyetlerinizi artırırken ekipmanınızın ömrünü de önemli ölçüde kısaltır.
Şaft hizalama hatalarının neden olduğu başlıca sorunlar şunlardır:
Makine genelinde artan titreşimler
Conta ve yataklarda aşırı ve hızlanmış aşınma
Mil veya kaplinde meydana gelen yapısal arızalar
Ekipman içindeki sürtünmenin artması
Daha yüksek enerji tüketimi
Yağ sızıntılarında artış
Civatalarda gevşeme
Kayış sistemlerinde aşınma ve beklenmedik arızalar
Şaft hizalaması öncesinde ve sırasında mutlaka "yumuşak ayak" analizini gerçekleştirmelisiniz. Yumuşak ayak terimi, dönen ekipmanın bir veya daha fazla ayağının montaj plakasıyla tam temas etmemesi durumunu tanımlar. Düzgün desteklenmeyen montaj parçaları, çalışma sırasında çatlayabilir ve bu durum hem hizalama sorunlarına hem de aşırı titreşimlere neden olabilir.
Pompa veya dişli kutusu montajlarında lazer hizalama sistemlerini kullanmak, yumuşak ayak problemlerini çözmek ve mükemmel şaft hizalaması elde etmek için en etkili yöntemdir. Doğru bir hizalama, dönen ekipmanınızın ömrünü uzatır, erken arızaları önler ve toplam bakım sürelerini önemli ölçüde azaltır.
Bu örnek, endüstriyel makine bakımının, plansız duruş sürelerini minimize etmenin yanı sıra etkin ekipman yönetiminin temel hedeflerine nasıl katkıda bulunduğunu mükemmel bir şekilde göstermektedir.
Makine Bakımını Bir Üst Seviyeye Taşımak
Kapsamlı bir Güvenilirlik Merkezli Bakım (RCM) programını hayata geçirmek, operasyonlarınızın çalışma süresini artıracak, ekipman güvenilirliğini yükseltecek ve bakım harcamalarını azaltacaktır. Eğer tam kapsamlı bir RCM programı mali imkânlarınızın ötesindeyse, 80/20 prensibini uygulayabilirsiniz.
Bu prensibin temel düşüncesi şudur: Bakım kazancınızın %80'i, günlük olarak gerçekleştirdiğiniz önleyici eylemlerin sadece %20'sinden gelecektir. Yani, az sayıdaki kritik ve stratejik bakım faaliyeti, toplam performansınızın büyük kısmını belirleyecektir.
Etkili bir bakım programının temelini oluşturan ve bireysel olarak uygulayabileceğiniz temel stratejileri özetledik. Bu yaklaşımlar, bakım yönetimini dönüştürebilir ve operasyonel verimliliğinizi önemli ölçüde artırabilir.
Limble CMMS, bakım bakımını organize etmek, otomatikleştirmek ve kolaylaştırmak için tasarlanmıştır. Nasıl yapılacağını öğrenmek için bir demo talep edin , ücretsiz bir deneme başlatın.
Makinelerinizin düzenli ve etkili bakımı, onlardan daha fazla verim almanızı ve daha uzun süre faydalanmanızı sağlar. Endüstride en üst düzey yaklaşım olarak kabul edilen Güvenilirlik Merkezli Bakım (RCM) sistemi, ideal bir çözüm sunsa da, uygulanması için ciddi bir bütçe ve yönetimsel kaynak gerektirir.
RCM sistemini kurmak şu an için işletmeniz açısından uygun değilse endişelenmeyin. Size burada, çok fazla maliyet gerektirmeden makine bakım süreçlerinizi iyileştirebileceğiniz sekiz temel prensip sunacağız.
1) Basit bir kondisyon izleme sistemi uygulayın
Çoğu ekipman, ciddi bir arızadan veya performans düşüşünden çok önce belirgin bozulma sinyalleri verir. Performans görünür şekilde etkilenmeden ve ürün kalitesi düşmeden, makine zaten sıkıntı yaşadığını size söyleyecektir.
Kondisyon izleme, bir makinedeki belirli koşulların gözlemlenmesi ve olası arızalara işaret edebilecek değişikliklerin tespit edilmesi anlamına gelir. Bu yaklaşım, potansiyel sorunları önceden fark etmenize ve bakım müdahalelerini zamanında planlamanıza olanak sağlar.
Kritik bir makine parçası için şu soruları yanıtlamanız gerekiyor:
Erken tehlike sinyallerini nasıl yakalayabilirim?
İzlemem gereken 1-2 temel parametre nedir?
Örneğin:
Titreşim seviyesi
Sıcaklık değişimleri
Gürültü düzeyi
Yağ kalitesi
Elektriksel tüketim
AirGemba'nın IoT ve yapay zeka destekli platformu, titreşim analizi gibi kondisyon izleme süreçlerini otomatikleştirerek:
Arızaları önceden tespit etmenize
Ekipman sağlığını gerçek zamanlı izlemenize
Tahmin edilebilir bakım stratejileri geliştirmenize
Beklenmedik duruş sürelerini minimize etmenize yardımcı olur
Bu yaklaşım, reaktif bakımdan proaktif bakıma geçişin anahtarıdır.
2) Operatörler için ekipman günlüklerini tanıtın ve eğitin
Makine operatörleriniz, arızaları önlemede en ön cephede yer alır. Her gün makinelerle çalıştıkları için, bir makinenin düzgün çalışıp çalışmadığını görünüşünden ve sesinden hemen anlayabilirler.
Ancak şu gerçeği de göz ardı edemeyiz: Ekipman arızalarının en yaygın sebeplerinden biri operatör hatalarıdır. Bu yüzden tüm operatörlerin makineleri doğru kullanması hayati önem taşır.
Bunu sağlamak için şunları yapmanızı öneriyoruz:
Öncelikle, güvenli ve verimli makine kullanımı için standart bir çalışma prosedürü oluşturun ve operatörlerinizi bu konuda eğitin. Onlara sık karşılaşılan sorunları nasıl fark edeceklerini öğretin. Temizlik ve yağlama gibi günlük basit bakım işlerini de sorumlulukları arasına ekleyin. Kısacası, bakım sorumluluğunun bir kısmını operatörlere devrederek 'otonom bakım' sistemine geçmeyi hedefleyin.
Operatörlerin işini kolaylaştırmak için makine günlüğü sistemi kurun. Bu günlüklere gözlemlerini, endişelerini ve karşılaştıkları sorunları not edebilsinler. Bakım ekibiniz bu günlükleri her gün kontrol etmeli ve notları şu üç kategoriden birine göre değerlendirmelidir:
Önemsiz bir durum - herhangi bir işlem gerektirmez
Hemen çözülebilecek basit bir sorun - teknisyen hemen müdahale eder
Planlı bakımda ele alınması gereken bir konu - bakım planına eklenir ve takip için iş emri numarası günlüğe işlenir
3) Planlı bakım görev kitleri geliştirin
Planlı bakımlarda genellikle aynı parçalar ve sarf malzemeleri tekrar tekrar kullanılır. Bu durumda, teknisyenin her bakım öncesi gerekli malzemeleri tek tek toplaması yerine, daha pratik bir yöntem öneriyoruz:
Bakım kitleri hazırlayın. Her kit, belirli bir bakım görevi için gereken tüm parça ve malzemeleri içersin. Bu kitlere özel parça numaraları verin ve planlı bakım formlarında bu numaraları kullanın. Böylece hem takip kolaylaşır, hem de karışıklık riski azalır.
Bu sistem sayesinde, bir bakım planlandığında depo görevliniz ilgili kiti raftan alıp hazırlayabilir. Bakım günü geldiğinde de teknisyenleriniz, o gün yapacakları tüm bakım işleri için gereken kitleri toplu halde teslim alır ve vakit kaybetmeden işe başlayabilir."
Bu düzenlemede ana fikri korurken, daha doğal bir Türkçe anlatım kullandım ve içeriği daha organize bir şekilde sundum. Teknik terimleri muhafaza ederken, anlatımı daha akıcı hale getirdim.
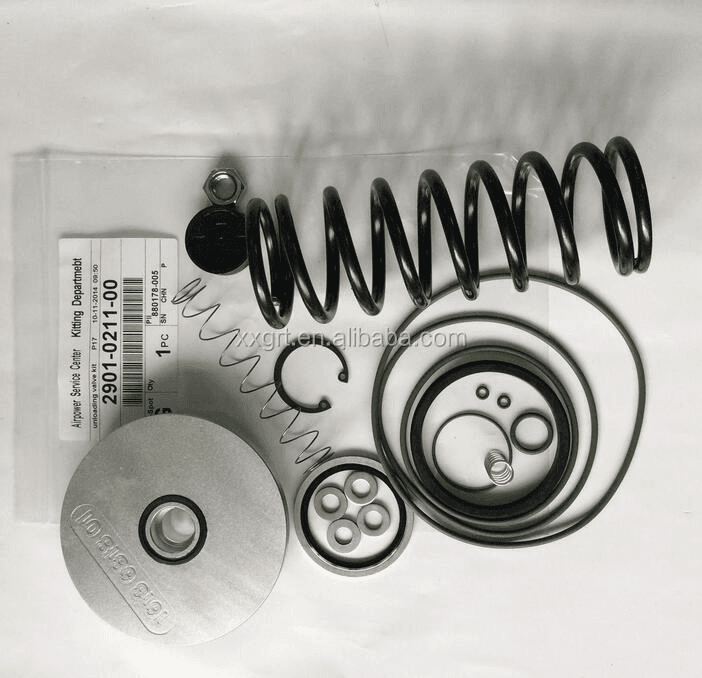
FS 8000H OEM Hava Kompresörü için önleyici bakım kiti.
Önceden hazırlanmış bakım kitleri, birçok açıdan işinizi kolaylaştırır. Öncelikle, planlı bakım başlamadan önce tüm gerekli malzemelerin elinizin altında olmasını sağlar. Bu da teknisyenlerinizin zamanını verimli kullanmalarına yardımcı olur.
Dahası, bu sistem sayesinde yağlama veya conta değiştirme gibi küçük ama kritik bakım işleri de atlanmaz. Çünkü teknisyenin eksik malzeme aramak için atölyeden ayrılması gerekmez ve tüm işler planlandığı gibi yapılabilir.
4) Performans metriklerini takip edin
Bakım programınızın verimli çalıştığını düşünseniz bile, düzenli bakım işlemlerini aksatmak, uzun vadede makinelerinizin güvenilirliğini ve ömrünü ciddi şekilde etkileyebilir. İdeal bir senaryoda, önleyici bakımı düzenli yaparak sadece birkaç acil müdahale gerektiren arıza ile karşılaşırız.
Ancak gerçek hayatta, güvenilmez ekipmanlarla uğraşırken daha sık arızalarla karşılaşmak kaçınılmaz oluyor. Bakım performansını izlemek, planlı bakım görevlerinin tam zamanında ve gerekli sıklıkta yapılıp yapılmadığını anlamak için çok önemli bir yöntem.
Bu izleme sayesinde, bakım iş listenizdeki görevlerin tamamlanma durumunu ve ekipmanlarınızın toplam arıza sürelerini net bir şekilde görebilirsiniz. Ayrıca, sık yaşanan arızaları tespit edebilir ve buna göre önlemler alabilirsiniz. Bu bilgileri kullanarak, önleyici bakım sıklığını artırabilir veya ekipmanlarınızın güvenilirliğini yükseltecek ek çalışmalar yapabilirsiniz.
İşte bakım performansınızı değerlendirebileceğiniz beş temel gösterge:
Aylık olarak planlanan bakım görevlerine kıyasla tamamlanan görev sayısı
Aylık meydana gelen arıza sayısı
Arızaların ekipman türüne veya konumuna göre nedenleri
Aylık olarak bakım iş listesine eklenen ve çıkarılan görev sayısı
Ortalama arıza onarım süresi (MTTR) ve ortalama arıza aralığı (MTBF)
Bu bakım metriklerini düzenli olarak takip ederek, bakım stratejinizin gelişip gelişmediğini veya gerilediğini görebilirsiniz. Böylece, sisteminizdeki potansiyel sorunları erkenden tespit edebilir ve gerekli düzeltmeleri yapabilirsiniz.
5) Modern bir CMMS ile makine bakımını kolaylaştırın
Ekipman performansınız ve bakım prosedürleriniz hakkında veri toplayamıyorsanız, esasen gözü bağlı bir şekilde çalışıyor ve operasyonunuzu optimize etmek için boşuna çırpınıyorsunuz demektir. Bilgisayar destekli bir bakım yönetim sistemini (CMMS) uygulamak, birkaç yıl öncesine kıyasla artık çok daha kolay. Üstelik bakım performansınız hakkında elde edeceğiniz içgörüler, yatırımın karşılığını fazlasıyla verecek.
Modern bir CMMS'ye geçmek, operasyonel verileri yakalamaya ve bakım faaliyetlerini yönetmeye başlamanın uygun maliyetli ve etkili bir yoludur. Günümüz bulut tabanlı bakım yazılımları, işletmelere oldukça güçlü özellikler sunuyor:
Önleyici bakım takvimi ve zamanlaması: Bakım işlemlerinizi önceden planlamanıza ve düzenli olarak gerçekleştirmenize olanak sağlar.
Yedek parça envanter yönetimi: Stok durumunuzu anında görmenizi ve parça eksikliği riskini minimize etmenizi sağlar.
Varlık Yönetimi: Tüm ekipmanlarınızın yaşam döngüsünü izlemenize ve performanslarını takip etmenize yardımcı olur.
İş emri yönetimi: Bakım görevlerinin atanması, takibi ve tamamlanması süreçlerini kolaylaştırır.
Detaylı Raporlama: Performans ve bakım verilerinizi analiz etmenize olanak tanır.
Üstelik modern CMMS sistemleri, finans ve insan kaynakları gibi diğer iş çözümleriyle de entegre olabilmektedir. Dahası, makine sensörlerinden gerçek zamanlı veri toplama özelliği sayesinde, ekipmanlarınızın durumunu anında izleyebilirsiniz.
6) Planlı Bakım görevlerini optimize edin
Planlı bakım görevleri genellikle "kur ve unut" yaklaşımıyla ele alınır - bir kez oluşturulduktan sonra neredeyse hiç gözden geçirilmezler. Oysa tüm planlı bakım görevlerini sürekli olarak gözden geçirmek, bakım stratejinizin en kritik parçasıdır.
Her bir bakım görevini aşağıdaki açılardan düzenli olarak değerlendirmek şart:
Güncelliği: Bu göreve hâlâ ihtiyaç var mı? Eğer artık gerekli değilse, derhal listeden çıkarın.
Etkinliği: Tanımlanan görev gerçekten en etkili yaklaşım mı? Belki de süreç daha fazla ayrıntıya veya daha az adıma ihtiyaç duyuyor olabilir.
Verimliliği: Görevi daha optimize edebilir misiniz? Aynı sonucu daha az kaynak ve zamanda elde etmenin yolları var mı?
Doğruluğu: Görev, doğru teknik kılavuzlara ve gerekli yedek parça bilgilerine mi atıfta bulunuyor?
Planlama Süresi: Göreve ayrılan zaman gerçekçi mi? Fazla mı tahmin edilmiş yoksa eksik mi planlanmış? Ayrıca, bu görevi gerçekleştirecek personel hâlâ uygun ve yetkin mi?
Görev Çakışmaları: Benzer veya örtüşen başka görevler var mı? Belki bunları birleştirmenin zamanı gelmiştir.
Eksik Alanlar: Verileriniz yeni bir önleyici bakım görevine ihtiyaç olduğunu mı gösteriyor? Henüz bakım kapsamına alınmamış ekipmanlar var mı?
Optimize etme sürecinde, standartlaştırılabilecek görevleri belirleyin. Bunun için özel önleyici bakım kontrol listeleri oluşturun ve bunları bakım planlarınıza entegre edin.
Sürekli iyileştirme kültürünü benimsemek, bakım programınızda küçük ama sürekli güncellemeler yapmanıza olanak sağlar. Bu yaklaşım, bakım yatırımınızdan maksimum verimi almanızın anahtarıdır.
7) Bir yağlama programı oluşturun
Yağlamayı sıradan bakım görevlerinin içine gömmek yerine, her ekipmanın zamanında ve doğru şekilde yağlanmasını sağlayacak bağımsız bir yağlama programı oluşturmak çok önemlidir. Böyle bir program, ekipmanlarınızın performansını ve ömrünü doğrudan etkileyecektir.
Kapsamlı bir yağlama programı oluşturmak için şu adımları izleyin:
Yağlama Noktalarının Tespiti: Tüm yağlama noktalarını detaylı bir şekilde tespit edin, kaydedin ve haritalandırın. Bu süreç özellikle eski makinelerde oldukça zahmetli olabilir, ancak mutlaka yapılması gereken bir çalışmadır.
Dinamik Yağlama Planlaması: Makine çalışma saatlerini ve üretim döngülerini dikkate alın. Yağlama ihtiyacı, makine kullanım yoğunluğuna ve türüne bağlı olarak değişkenlik gösterir.
Yağ Değişimi ve Analizi: Her yağ değişimini programınıza dahil edin. Alınan yağ numunelerinin sonuçlarını düzenli olarak analiz edin. Bu, olası arızaların erken tespitine yardımcı olacaktır.
Doğru Yağlayıcı Seçimi: Her ekipman için:
Uygun yağlayıcı türünü belirleyin
Gerekli yağlayıcı miktarını tespit edin
Yağlama prosedürünü net bir şekilde tanımlayın
Düzeltici Bakım: Yağlama noktalarında herhangi bir hasar, tıkanıklık veya deformasyon tespit edildiğinde hemen müdahale edilmesini sağlayın.
Maksimum ekipman ömrüne ulaşmak birçok faktöre bağlı olsa da, güvenilirliği artıran en temel eylemlerden biri kesinlikle kapsamlı ve sistematik bir yağlama programıdır. Bu programa yatırım yapmak, uzun vadede ciddi maliyet tasarrufları ve performans artışı sağlayacaktır.
8) Pompa ve dişli kutularında yumuşak ayak analizi ve mil hizalaması yapın
Dönen makinelerde şaft hizalamasındaki hatalar, işletmeniz için ciddi sonuçlar doğurabilecek bir dizi probleme yol açar. Yanlış hizalanmış bir şaft, bakım maliyetlerinizi artırırken ekipmanınızın ömrünü de önemli ölçüde kısaltır.
Şaft hizalama hatalarının neden olduğu başlıca sorunlar şunlardır:
Makine genelinde artan titreşimler
Conta ve yataklarda aşırı ve hızlanmış aşınma
Mil veya kaplinde meydana gelen yapısal arızalar
Ekipman içindeki sürtünmenin artması
Daha yüksek enerji tüketimi
Yağ sızıntılarında artış
Civatalarda gevşeme
Kayış sistemlerinde aşınma ve beklenmedik arızalar
Şaft hizalaması öncesinde ve sırasında mutlaka "yumuşak ayak" analizini gerçekleştirmelisiniz. Yumuşak ayak terimi, dönen ekipmanın bir veya daha fazla ayağının montaj plakasıyla tam temas etmemesi durumunu tanımlar. Düzgün desteklenmeyen montaj parçaları, çalışma sırasında çatlayabilir ve bu durum hem hizalama sorunlarına hem de aşırı titreşimlere neden olabilir.
Pompa veya dişli kutusu montajlarında lazer hizalama sistemlerini kullanmak, yumuşak ayak problemlerini çözmek ve mükemmel şaft hizalaması elde etmek için en etkili yöntemdir. Doğru bir hizalama, dönen ekipmanınızın ömrünü uzatır, erken arızaları önler ve toplam bakım sürelerini önemli ölçüde azaltır.
Bu örnek, endüstriyel makine bakımının, plansız duruş sürelerini minimize etmenin yanı sıra etkin ekipman yönetiminin temel hedeflerine nasıl katkıda bulunduğunu mükemmel bir şekilde göstermektedir.
Makine Bakımını Bir Üst Seviyeye Taşımak
Kapsamlı bir Güvenilirlik Merkezli Bakım (RCM) programını hayata geçirmek, operasyonlarınızın çalışma süresini artıracak, ekipman güvenilirliğini yükseltecek ve bakım harcamalarını azaltacaktır. Eğer tam kapsamlı bir RCM programı mali imkânlarınızın ötesindeyse, 80/20 prensibini uygulayabilirsiniz.
Bu prensibin temel düşüncesi şudur: Bakım kazancınızın %80'i, günlük olarak gerçekleştirdiğiniz önleyici eylemlerin sadece %20'sinden gelecektir. Yani, az sayıdaki kritik ve stratejik bakım faaliyeti, toplam performansınızın büyük kısmını belirleyecektir.
Etkili bir bakım programının temelini oluşturan ve bireysel olarak uygulayabileceğiniz temel stratejileri özetledik. Bu yaklaşımlar, bakım yönetimini dönüştürebilir ve operasyonel verimliliğinizi önemli ölçüde artırabilir.
Limble CMMS, bakım bakımını organize etmek, otomatikleştirmek ve kolaylaştırmak için tasarlanmıştır. Nasıl yapılacağını öğrenmek için bir demo talep edin , ücretsiz bir deneme başlatın.
Makinelerinizin düzenli ve etkili bakımı, onlardan daha fazla verim almanızı ve daha uzun süre faydalanmanızı sağlar. Endüstride en üst düzey yaklaşım olarak kabul edilen Güvenilirlik Merkezli Bakım (RCM) sistemi, ideal bir çözüm sunsa da, uygulanması için ciddi bir bütçe ve yönetimsel kaynak gerektirir.
RCM sistemini kurmak şu an için işletmeniz açısından uygun değilse endişelenmeyin. Size burada, çok fazla maliyet gerektirmeden makine bakım süreçlerinizi iyileştirebileceğiniz sekiz temel prensip sunacağız.
1) Basit bir kondisyon izleme sistemi uygulayın
Çoğu ekipman, ciddi bir arızadan veya performans düşüşünden çok önce belirgin bozulma sinyalleri verir. Performans görünür şekilde etkilenmeden ve ürün kalitesi düşmeden, makine zaten sıkıntı yaşadığını size söyleyecektir.
Kondisyon izleme, bir makinedeki belirli koşulların gözlemlenmesi ve olası arızalara işaret edebilecek değişikliklerin tespit edilmesi anlamına gelir. Bu yaklaşım, potansiyel sorunları önceden fark etmenize ve bakım müdahalelerini zamanında planlamanıza olanak sağlar.
Kritik bir makine parçası için şu soruları yanıtlamanız gerekiyor:
Erken tehlike sinyallerini nasıl yakalayabilirim?
İzlemem gereken 1-2 temel parametre nedir?
Örneğin:
Titreşim seviyesi
Sıcaklık değişimleri
Gürültü düzeyi
Yağ kalitesi
Elektriksel tüketim
AirGemba'nın IoT ve yapay zeka destekli platformu, titreşim analizi gibi kondisyon izleme süreçlerini otomatikleştirerek:
Arızaları önceden tespit etmenize
Ekipman sağlığını gerçek zamanlı izlemenize
Tahmin edilebilir bakım stratejileri geliştirmenize
Beklenmedik duruş sürelerini minimize etmenize yardımcı olur
Bu yaklaşım, reaktif bakımdan proaktif bakıma geçişin anahtarıdır.
2) Operatörler için ekipman günlüklerini tanıtın ve eğitin
Makine operatörleriniz, arızaları önlemede en ön cephede yer alır. Her gün makinelerle çalıştıkları için, bir makinenin düzgün çalışıp çalışmadığını görünüşünden ve sesinden hemen anlayabilirler.
Ancak şu gerçeği de göz ardı edemeyiz: Ekipman arızalarının en yaygın sebeplerinden biri operatör hatalarıdır. Bu yüzden tüm operatörlerin makineleri doğru kullanması hayati önem taşır.
Bunu sağlamak için şunları yapmanızı öneriyoruz:
Öncelikle, güvenli ve verimli makine kullanımı için standart bir çalışma prosedürü oluşturun ve operatörlerinizi bu konuda eğitin. Onlara sık karşılaşılan sorunları nasıl fark edeceklerini öğretin. Temizlik ve yağlama gibi günlük basit bakım işlerini de sorumlulukları arasına ekleyin. Kısacası, bakım sorumluluğunun bir kısmını operatörlere devrederek 'otonom bakım' sistemine geçmeyi hedefleyin.
Operatörlerin işini kolaylaştırmak için makine günlüğü sistemi kurun. Bu günlüklere gözlemlerini, endişelerini ve karşılaştıkları sorunları not edebilsinler. Bakım ekibiniz bu günlükleri her gün kontrol etmeli ve notları şu üç kategoriden birine göre değerlendirmelidir:
Önemsiz bir durum - herhangi bir işlem gerektirmez
Hemen çözülebilecek basit bir sorun - teknisyen hemen müdahale eder
Planlı bakımda ele alınması gereken bir konu - bakım planına eklenir ve takip için iş emri numarası günlüğe işlenir
3) Planlı bakım görev kitleri geliştirin
Planlı bakımlarda genellikle aynı parçalar ve sarf malzemeleri tekrar tekrar kullanılır. Bu durumda, teknisyenin her bakım öncesi gerekli malzemeleri tek tek toplaması yerine, daha pratik bir yöntem öneriyoruz:
Bakım kitleri hazırlayın. Her kit, belirli bir bakım görevi için gereken tüm parça ve malzemeleri içersin. Bu kitlere özel parça numaraları verin ve planlı bakım formlarında bu numaraları kullanın. Böylece hem takip kolaylaşır, hem de karışıklık riski azalır.
Bu sistem sayesinde, bir bakım planlandığında depo görevliniz ilgili kiti raftan alıp hazırlayabilir. Bakım günü geldiğinde de teknisyenleriniz, o gün yapacakları tüm bakım işleri için gereken kitleri toplu halde teslim alır ve vakit kaybetmeden işe başlayabilir."
Bu düzenlemede ana fikri korurken, daha doğal bir Türkçe anlatım kullandım ve içeriği daha organize bir şekilde sundum. Teknik terimleri muhafaza ederken, anlatımı daha akıcı hale getirdim.
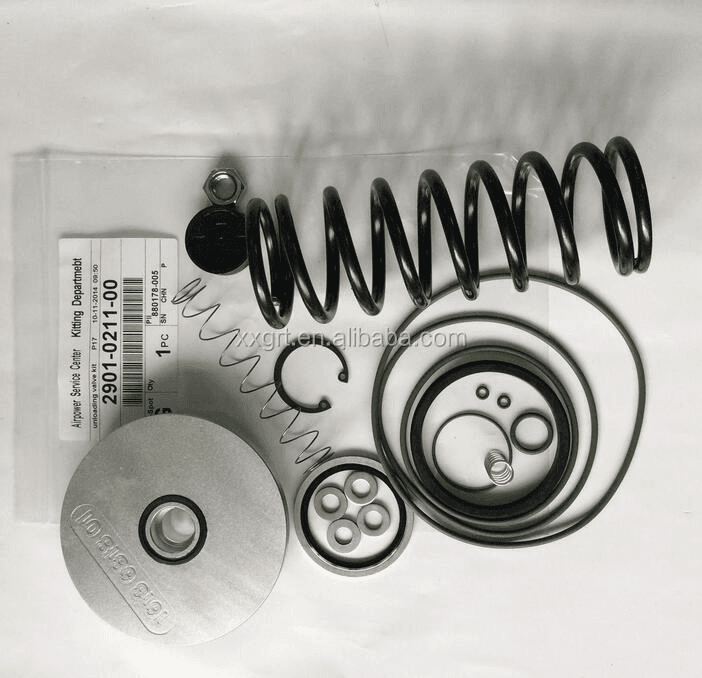
FS 8000H OEM Hava Kompresörü için önleyici bakım kiti.
Önceden hazırlanmış bakım kitleri, birçok açıdan işinizi kolaylaştırır. Öncelikle, planlı bakım başlamadan önce tüm gerekli malzemelerin elinizin altında olmasını sağlar. Bu da teknisyenlerinizin zamanını verimli kullanmalarına yardımcı olur.
Dahası, bu sistem sayesinde yağlama veya conta değiştirme gibi küçük ama kritik bakım işleri de atlanmaz. Çünkü teknisyenin eksik malzeme aramak için atölyeden ayrılması gerekmez ve tüm işler planlandığı gibi yapılabilir.
4) Performans metriklerini takip edin
Bakım programınızın verimli çalıştığını düşünseniz bile, düzenli bakım işlemlerini aksatmak, uzun vadede makinelerinizin güvenilirliğini ve ömrünü ciddi şekilde etkileyebilir. İdeal bir senaryoda, önleyici bakımı düzenli yaparak sadece birkaç acil müdahale gerektiren arıza ile karşılaşırız.
Ancak gerçek hayatta, güvenilmez ekipmanlarla uğraşırken daha sık arızalarla karşılaşmak kaçınılmaz oluyor. Bakım performansını izlemek, planlı bakım görevlerinin tam zamanında ve gerekli sıklıkta yapılıp yapılmadığını anlamak için çok önemli bir yöntem.
Bu izleme sayesinde, bakım iş listenizdeki görevlerin tamamlanma durumunu ve ekipmanlarınızın toplam arıza sürelerini net bir şekilde görebilirsiniz. Ayrıca, sık yaşanan arızaları tespit edebilir ve buna göre önlemler alabilirsiniz. Bu bilgileri kullanarak, önleyici bakım sıklığını artırabilir veya ekipmanlarınızın güvenilirliğini yükseltecek ek çalışmalar yapabilirsiniz.
İşte bakım performansınızı değerlendirebileceğiniz beş temel gösterge:
Aylık olarak planlanan bakım görevlerine kıyasla tamamlanan görev sayısı
Aylık meydana gelen arıza sayısı
Arızaların ekipman türüne veya konumuna göre nedenleri
Aylık olarak bakım iş listesine eklenen ve çıkarılan görev sayısı
Ortalama arıza onarım süresi (MTTR) ve ortalama arıza aralığı (MTBF)
Bu bakım metriklerini düzenli olarak takip ederek, bakım stratejinizin gelişip gelişmediğini veya gerilediğini görebilirsiniz. Böylece, sisteminizdeki potansiyel sorunları erkenden tespit edebilir ve gerekli düzeltmeleri yapabilirsiniz.
5) Modern bir CMMS ile makine bakımını kolaylaştırın
Ekipman performansınız ve bakım prosedürleriniz hakkında veri toplayamıyorsanız, esasen gözü bağlı bir şekilde çalışıyor ve operasyonunuzu optimize etmek için boşuna çırpınıyorsunuz demektir. Bilgisayar destekli bir bakım yönetim sistemini (CMMS) uygulamak, birkaç yıl öncesine kıyasla artık çok daha kolay. Üstelik bakım performansınız hakkında elde edeceğiniz içgörüler, yatırımın karşılığını fazlasıyla verecek.
Modern bir CMMS'ye geçmek, operasyonel verileri yakalamaya ve bakım faaliyetlerini yönetmeye başlamanın uygun maliyetli ve etkili bir yoludur. Günümüz bulut tabanlı bakım yazılımları, işletmelere oldukça güçlü özellikler sunuyor:
Önleyici bakım takvimi ve zamanlaması: Bakım işlemlerinizi önceden planlamanıza ve düzenli olarak gerçekleştirmenize olanak sağlar.
Yedek parça envanter yönetimi: Stok durumunuzu anında görmenizi ve parça eksikliği riskini minimize etmenizi sağlar.
Varlık Yönetimi: Tüm ekipmanlarınızın yaşam döngüsünü izlemenize ve performanslarını takip etmenize yardımcı olur.
İş emri yönetimi: Bakım görevlerinin atanması, takibi ve tamamlanması süreçlerini kolaylaştırır.
Detaylı Raporlama: Performans ve bakım verilerinizi analiz etmenize olanak tanır.
Üstelik modern CMMS sistemleri, finans ve insan kaynakları gibi diğer iş çözümleriyle de entegre olabilmektedir. Dahası, makine sensörlerinden gerçek zamanlı veri toplama özelliği sayesinde, ekipmanlarınızın durumunu anında izleyebilirsiniz.
6) Planlı Bakım görevlerini optimize edin
Planlı bakım görevleri genellikle "kur ve unut" yaklaşımıyla ele alınır - bir kez oluşturulduktan sonra neredeyse hiç gözden geçirilmezler. Oysa tüm planlı bakım görevlerini sürekli olarak gözden geçirmek, bakım stratejinizin en kritik parçasıdır.
Her bir bakım görevini aşağıdaki açılardan düzenli olarak değerlendirmek şart:
Güncelliği: Bu göreve hâlâ ihtiyaç var mı? Eğer artık gerekli değilse, derhal listeden çıkarın.
Etkinliği: Tanımlanan görev gerçekten en etkili yaklaşım mı? Belki de süreç daha fazla ayrıntıya veya daha az adıma ihtiyaç duyuyor olabilir.
Verimliliği: Görevi daha optimize edebilir misiniz? Aynı sonucu daha az kaynak ve zamanda elde etmenin yolları var mı?
Doğruluğu: Görev, doğru teknik kılavuzlara ve gerekli yedek parça bilgilerine mi atıfta bulunuyor?
Planlama Süresi: Göreve ayrılan zaman gerçekçi mi? Fazla mı tahmin edilmiş yoksa eksik mi planlanmış? Ayrıca, bu görevi gerçekleştirecek personel hâlâ uygun ve yetkin mi?
Görev Çakışmaları: Benzer veya örtüşen başka görevler var mı? Belki bunları birleştirmenin zamanı gelmiştir.
Eksik Alanlar: Verileriniz yeni bir önleyici bakım görevine ihtiyaç olduğunu mı gösteriyor? Henüz bakım kapsamına alınmamış ekipmanlar var mı?
Optimize etme sürecinde, standartlaştırılabilecek görevleri belirleyin. Bunun için özel önleyici bakım kontrol listeleri oluşturun ve bunları bakım planlarınıza entegre edin.
Sürekli iyileştirme kültürünü benimsemek, bakım programınızda küçük ama sürekli güncellemeler yapmanıza olanak sağlar. Bu yaklaşım, bakım yatırımınızdan maksimum verimi almanızın anahtarıdır.
7) Bir yağlama programı oluşturun
Yağlamayı sıradan bakım görevlerinin içine gömmek yerine, her ekipmanın zamanında ve doğru şekilde yağlanmasını sağlayacak bağımsız bir yağlama programı oluşturmak çok önemlidir. Böyle bir program, ekipmanlarınızın performansını ve ömrünü doğrudan etkileyecektir.
Kapsamlı bir yağlama programı oluşturmak için şu adımları izleyin:
Yağlama Noktalarının Tespiti: Tüm yağlama noktalarını detaylı bir şekilde tespit edin, kaydedin ve haritalandırın. Bu süreç özellikle eski makinelerde oldukça zahmetli olabilir, ancak mutlaka yapılması gereken bir çalışmadır.
Dinamik Yağlama Planlaması: Makine çalışma saatlerini ve üretim döngülerini dikkate alın. Yağlama ihtiyacı, makine kullanım yoğunluğuna ve türüne bağlı olarak değişkenlik gösterir.
Yağ Değişimi ve Analizi: Her yağ değişimini programınıza dahil edin. Alınan yağ numunelerinin sonuçlarını düzenli olarak analiz edin. Bu, olası arızaların erken tespitine yardımcı olacaktır.
Doğru Yağlayıcı Seçimi: Her ekipman için:
Uygun yağlayıcı türünü belirleyin
Gerekli yağlayıcı miktarını tespit edin
Yağlama prosedürünü net bir şekilde tanımlayın
Düzeltici Bakım: Yağlama noktalarında herhangi bir hasar, tıkanıklık veya deformasyon tespit edildiğinde hemen müdahale edilmesini sağlayın.
Maksimum ekipman ömrüne ulaşmak birçok faktöre bağlı olsa da, güvenilirliği artıran en temel eylemlerden biri kesinlikle kapsamlı ve sistematik bir yağlama programıdır. Bu programa yatırım yapmak, uzun vadede ciddi maliyet tasarrufları ve performans artışı sağlayacaktır.
8) Pompa ve dişli kutularında yumuşak ayak analizi ve mil hizalaması yapın
Dönen makinelerde şaft hizalamasındaki hatalar, işletmeniz için ciddi sonuçlar doğurabilecek bir dizi probleme yol açar. Yanlış hizalanmış bir şaft, bakım maliyetlerinizi artırırken ekipmanınızın ömrünü de önemli ölçüde kısaltır.
Şaft hizalama hatalarının neden olduğu başlıca sorunlar şunlardır:
Makine genelinde artan titreşimler
Conta ve yataklarda aşırı ve hızlanmış aşınma
Mil veya kaplinde meydana gelen yapısal arızalar
Ekipman içindeki sürtünmenin artması
Daha yüksek enerji tüketimi
Yağ sızıntılarında artış
Civatalarda gevşeme
Kayış sistemlerinde aşınma ve beklenmedik arızalar
Şaft hizalaması öncesinde ve sırasında mutlaka "yumuşak ayak" analizini gerçekleştirmelisiniz. Yumuşak ayak terimi, dönen ekipmanın bir veya daha fazla ayağının montaj plakasıyla tam temas etmemesi durumunu tanımlar. Düzgün desteklenmeyen montaj parçaları, çalışma sırasında çatlayabilir ve bu durum hem hizalama sorunlarına hem de aşırı titreşimlere neden olabilir.
Pompa veya dişli kutusu montajlarında lazer hizalama sistemlerini kullanmak, yumuşak ayak problemlerini çözmek ve mükemmel şaft hizalaması elde etmek için en etkili yöntemdir. Doğru bir hizalama, dönen ekipmanınızın ömrünü uzatır, erken arızaları önler ve toplam bakım sürelerini önemli ölçüde azaltır.
Bu örnek, endüstriyel makine bakımının, plansız duruş sürelerini minimize etmenin yanı sıra etkin ekipman yönetiminin temel hedeflerine nasıl katkıda bulunduğunu mükemmel bir şekilde göstermektedir.
Makine Bakımını Bir Üst Seviyeye Taşımak
Kapsamlı bir Güvenilirlik Merkezli Bakım (RCM) programını hayata geçirmek, operasyonlarınızın çalışma süresini artıracak, ekipman güvenilirliğini yükseltecek ve bakım harcamalarını azaltacaktır. Eğer tam kapsamlı bir RCM programı mali imkânlarınızın ötesindeyse, 80/20 prensibini uygulayabilirsiniz.
Bu prensibin temel düşüncesi şudur: Bakım kazancınızın %80'i, günlük olarak gerçekleştirdiğiniz önleyici eylemlerin sadece %20'sinden gelecektir. Yani, az sayıdaki kritik ve stratejik bakım faaliyeti, toplam performansınızın büyük kısmını belirleyecektir.
Etkili bir bakım programının temelini oluşturan ve bireysel olarak uygulayabileceğiniz temel stratejileri özetledik. Bu yaklaşımlar, bakım yönetimini dönüştürebilir ve operasyonel verimliliğinizi önemli ölçüde artırabilir.
Limble CMMS, bakım bakımını organize etmek, otomatikleştirmek ve kolaylaştırmak için tasarlanmıştır. Nasıl yapılacağını öğrenmek için bir demo talep edin , ücretsiz bir deneme başlatın.